Maximizing Equipment Lifespan with Time-Based Maintenance Strategies
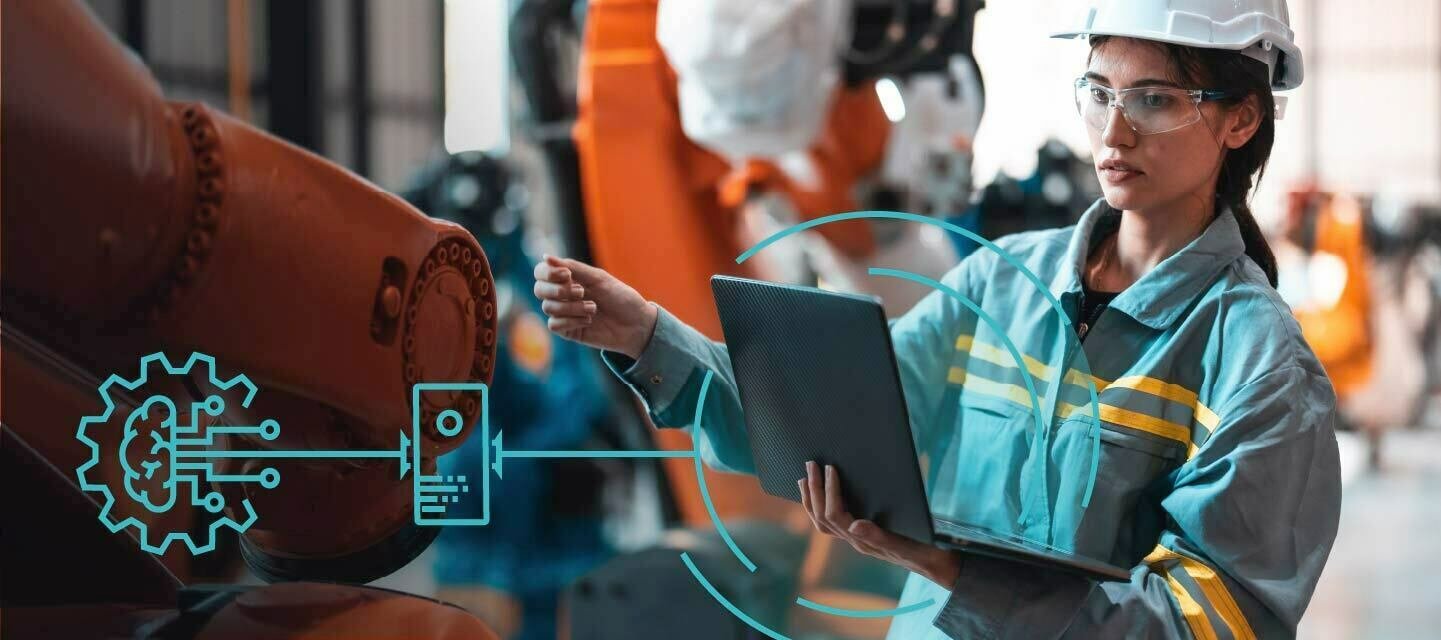
In today’s competitive industrial landscape, efficient asset management is not just beneficial—it’s essential for minimizing operational costs and maximizing equipment lifespan. One strategy that has proven to be highly effective in achieving these goals is time-based maintenance (TBM). By scheduling routine checks and interventions based on the passage of time, rather than waiting for failures or malfunctions to occur, organizations can prevent unexpected downtime, reduce repair costs, and extend the operational life of their machinery. In this post, we will delve deeper into how time-based maintenance works, the significant benefits it offers, and how industrial maintenance software can optimize this approach for a more streamlined operation.
Table of Contents
ToggleWhat Is Time-Based Maintenance?
Time-based maintenance refers to a preventive strategy wherein maintenance activities—such as inspections, replacements, or lubrication are performed at scheduled intervals. These intervals are typically determined by manufacturers’ recommendations or historical data on equipment usage. Unlike reactive maintenance, which addresses equipment issues only after failure, time-based maintenance ensures that machinery is serviced regularly to prevent breakdowns.
This strategy is particularly effective for non-critical assets or equipment that is easy to access. While it may not be suitable for every piece of machinery, TBM can significantly impact assets where failure could lead to minor disruptions or higher long-term costs.
The Many Benefits of Time-Based Maintenance
- Increased Equipment Reliability
One of the most significant advantages of implementing time-based maintenance is the enhanced reliability of equipment. Regular servicing keeps machines in optimal condition, reducing the likelihood of unexpected failures and costly downtime. A reliable machine not only boosts productivity but also enhances overall workplace safety. - Prolonged Asset Lifespan
Machinery represents a significant investment for any organization. By routinely performing preventive tasks—such as lubrication, tightening bolts, and replacing worn components—you can extend the life of your machinery. The longer your equipment lasts, the lower your overall capital expenditures will be over time. - Predictable Maintenance Costs
Scheduled interventions allow for better budgeting and financial planning. By moving away from a reactive maintenance approach, organizations can avoid the high costs associated with emergency repairs or unplanned downtime. Instead, you can predict and allocate resources effectively, reducing the financial strain on your operations. - Simplified Maintenance Planning
With a clear, time-based schedule in place, it’s easier to plan and allocate resources effectively. This ensures that the right personnel and necessary parts are available when maintenance is due, leading to efficient operations and fewer interruptions to production. - Compliance and Safety Assurance
Regular maintenance not only ensures equipment reliability but also contributes to compliance with industry regulations and safety standards. By keeping equipment in top shape, organizations can reduce the risk of accidents and maintain a safer work environment.
The Critical Role of Industrial Maintenance Software
While time-based maintenance is an effective strategy, managing these tasks manually can become increasingly challenging as an organization grows. This is where industrial maintenance software comes into play. Such software solutions automate the scheduling, tracking, and execution of maintenance activities, ensuring that no task is overlooked. Here are several ways it enhances the time-based maintenance approach:
- Automated Scheduling: The software generates maintenance schedules automatically based on predefined intervals. This ensures consistency across the entire operation, reducing the chance of human error and ensuring that no critical task is missed.
- Real-Time Tracking: With industrial maintenance software, you can track the status of each asset in real time. The software logs all maintenance activities, making it easier to monitor performance, identify recurring issues, and evaluate the effectiveness of your maintenance strategies.
- Data-Driven Insights: The software collects valuable data over time, which can be analyzed to uncover trends and insights. This analysis allows organizations to make informed decisions about maintenance intervals and resource allocation, ultimately leading to greater operational efficiency.
- Inventory Management: Many industrial maintenance software solutions come equipped with inventory management capabilities. This feature ensures that necessary parts and tools are always available when maintenance is due, further streamlining the maintenance process.
- User-Friendly Interfaces: Modern industrial maintenance software often includes intuitive interfaces that make it easier for maintenance teams to navigate and utilize the features effectively. This can lead to improved adoption rates and better overall results.
Implementing Time-Based Maintenance in Your Facility
To effectively implement time-based maintenance, follow these key steps:
- Select the Right Equipment for TBM
Not all equipment is suited for time-based maintenance. Identify the assets that will benefit most from routine inspections and interventions, focusing on machinery that operates continuously or on a predictable schedule. - Establish Maintenance Intervals
Use manufacturer guidelines and historical performance data to determine appropriate maintenance intervals for each piece of equipment. Consider factors such as operational hours, usage intensity, and environmental conditions. - Leverage Industrial Maintenance Software
Choose a software solution that aligns with your operational needs. Look for options that allow you to customize maintenance schedules, track performance, and manage inventory seamlessly. A good software solution will be an invaluable partner in your maintenance strategy. - Train Your Team
Ensure that your maintenance team is thoroughly familiar with both the time-based maintenance approach and the industrial maintenance software being used. Comprehensive training leads to smoother implementation and better overall results. - Monitor and Adjust
Regularly review your time-based maintenance program. Analyze data collected by your industrial maintenance software to evaluate the effectiveness of your maintenance schedules. Be prepared to make adjustments as necessary to optimize performance.
Conclusion
Time-based maintenance is a simple yet powerful approach to enhancing equipment reliability, extending lifespan, and controlling maintenance costs. With the help of industrial maintenance software, you can automate and streamline this process, improving efficiency and reducing the risk of human error. By adopting time-based maintenance strategies, your organization will be better equipped to meet production demands while keeping assets in peak condition for years to come.
Incorporating time-based maintenance not only boosts operational efficiency but also enhances your organization’s ability to respond to market demands, all while keeping your machinery performing at its best. The combination of strategic maintenance planning and modern industrial maintenance software can set your organization apart in a competitive landscape, leading to sustained growth and success.